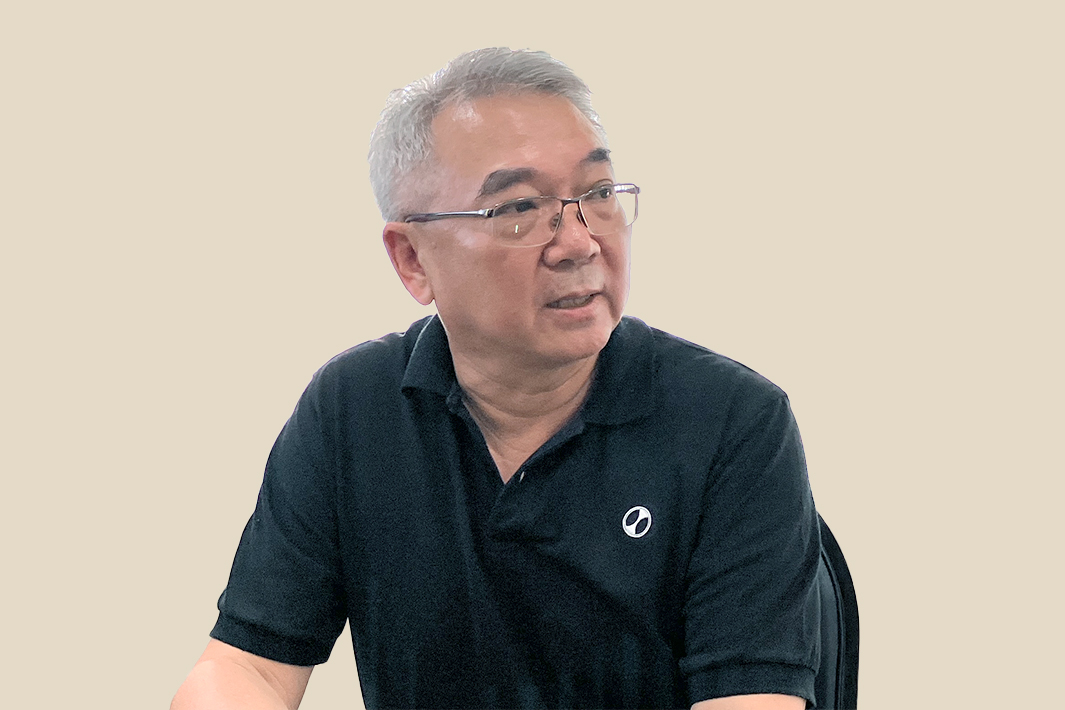
Since its establishment in 1998, Millcon Steel, a major electric furnace manufacturer in Thailand, has supported the country’s economic growth by producing and selling deformed steel bars, round bars and other products. In recent years, they have also been involved in producing and selling billets to manufacturers of special steel wire rods. They also operate an ELV (end-of-life vehicle) shredding plant and creating an integrated system from upstream to downstream. We recently interviewed to the company’s CEO Pravit Horungruang about the current business environment and outlook.
Q1 First, an overview of your business.
“In Thailand, we operate the Burapa Mill (in Rayong Province), which manages all steel rolling operations, and the Rama 2 Mill (in Bangkok), which is a single-pressure mill. We produce deformed steel bars and supply to domestic market and export some. The Burapa factory equip with a series of equipment, including one 75-ton electric furnace (EAF) manufactured by Italian company Danieli and a four-strand continuous casting and rolling mill. It produces wire diameters of 20mm or more, while the Rama 2 factory manufactures products with diameters of 20mm or less. We also supply billets for Kobelco Millcon Steel (Rayong Province), a joint venture with Kobe Steel.
Q2 Current demand trends.
“Domestic demand has remained sluggish due to a weak in the construction market and the influx of cheap Chinese steel materials, and production level is struggling at 30-40% of capacity. In addition to our company, In Thailand there are about ten electric furnace manufacturers and six induction furnace manufacturers operating, but they are also struggling with operating rates below 50%.
Q3 About the domestic scrap business.
“90% of the raw materials used at the Burapa factory are commercially generated products such as heavy scrap and HMS, as well as imported scrap, and approximately 10% of the total amount is supplied from Wastech which is our group. The purchase price of scrap is fixed by domestic demand and supply. Since there is no benchmark or price leader manufacturer, in most cases decisions are made between local scrap dealers and trading companies. Although we grasp HMS offer prices from USA to Turkey and P&S quotes, but we rarely use them as indicators in actual trading.
Q4 About Wastech, the shredder plant adjacent to the Burapa factory.
“We have one pre-shredder, one main shredder with 3,000 horsepower, and various sorting equipment, and supply the steel scrap recovered from ELV (end-of-life vehicles) to the Burapa factory. The shredder capacity is 25,000 to 30,000 tons per month, but the current actual result is around 10,000 tons, which is affected by the reduced production at the Burapa factory and the low demand. ELVs are pressed products (commonly known as car bundles) from South Korea and Australia. They are imported in containers, unloaded at the nearby Laem Chabang port, and transported here. The yield rate is approximately 70% iron and 30% dust. In Thailand, used cars are exported to Laos and Myanmar, so there is not established recycling flow for automobiles, all ELVs processed here are imported.
Q5 What about ASR (shredder dust) processing?
“We operate under the government’s license, and collect non-ferrous materials such as aluminum and copper, separate them into sizes using trommel. We sell them to specialized companies for 100% recycling. We thoroughly screen dust, it is highly rated for its excellent combustion efficiency.”
Q6 Demand outlook and challenges.
“The harsh environment is likely to continue for the time being due to sluggish construction demand and the influx of cheap Chinese materials. Thailand is known as the highest electricity costs in Southeast Asia. It is a major burden, so like Japan, most operations are performed at night. Thailand produces 5 million tons of steel annually using electric furnaces, and 70% of raw materials are procured domestically and the rest is imported. Although demand is low, domestically generated steel The quantity of scrap that can be used is limited, and there is intense competition among electric furnace manufacturers to collect scrap, so we would like to continue to focus on stable procurement.”